۱- مخلوط سنگ آهن ،کک (بیشتر کک را کربن تشکیل میدهد)، و سنگ آهک(کربنات کلسیم) به بالای کوره برده می شود
۲- پیستون بالای کوره پایین آمده و اجازه می دهد تا مواد اولیه به درون کوره رها شود
هوای گرم از پایین به جایی دمیده می شود که کوره ذوب آهن نام گرفته است این هوای گرم گاهی با اکسیژن تقویت می شود
۳- واکنش کک و اکسیژن در هوای گرم ،دی اکسید کربن و گرما ایجاد می کند.
۴- دی اکسید کربن تشکیل شده افزایش پیدامی کند با کک ورودی واکنش داده مونو اکسیدکربن تشکیل می دهد
۵- منو اکسید کربن ،اکسیژن را از اکسید آهن می گیرد و تشکیل آهن و دی اکسید کربن می دهد آهن ذوب شده به طرف ته کوره جاری می شود
۶- سنگ آهک به زدودن ناخالصی ها کمک می کند واکنش سنگ آهک با ناخالصی ها خاکستر یا سرباره را تشکیل می دهد سرباره عمدتا کلسیم سلیکات است که روی آهن ذوب شده شناور است و فلز را از اکسید شدن به وسیله هوای ورودی حفظ می کند آهن و سرباره با هم مخلوط نمی شوند و دو لایه جداگانه در ته کوره تشکیل می دهند
7- سرباره در فواصل معین از کوره خارج می شود از سرباره اغلب در ساخت جاده ها استفاده می شود
آهن نیز از راه دیگر خارج شده و بیشتر آهن به دست آمده از کوره در تهیه فولاد مورد استفاده قرار می گیرد.
در نمودارهای زیر کلیه مراحل استخراج آهن از سنگ معدن – فولاد سازی و مراحل ساخت قطعات فولادی را به صورت شماتیک نشان می دهد.

مواد اولیه مورد نیاز استخراج آهن
سنگ معدن آهن
در مجاورت ذغال بر اثر گرما در کوره احیا میشود و سپس بر اثر جریانی از گازهای احیا کننده داغ که از سوختن کک در هوای گرم پایین کوره تولید میشود و در جهت عکس مسیر آهن حرکت میکند، ذوب میشود. آهن مذاب و تفاله حاصل از سنگ معدن به ازای هر دو تا چهار ساعت از آتشدان کوره تخلیه میشود. اگر مواد اولیه بطور پیوسته از بالای کوره وارد شود، در این صورت ، کوره میتواند بطور پیوسته کار کند. محصول کوره وزشی همان چدن است که برای تبدیل آن به دیگر مشتقات آهن ، بویژه فولاد ، باید در آن تغییراتی داد.
زغال کک
مشخصات ساختاری آن عبارت است از : کربن ثابت 85 تا 90 درصد ، خاکستر 5 تا 13 درصد ، رطوبت تا 8 درصد ، مواد فرّار 1.6 تا 11 درصد ، و گوگرد 0.5 تا 1.2 درصد. نقش کک در فرآیند کورههای وزشی تولید گازهای احیا کننده است و در اثر سوختن در پایین کوره انجام میپذیرد و مقاومت مکانیکی آن نیز در عمل مهم است. اندازه کک مورد مصرف ، باید بین 1.5 تا 75 میلیمتر باشد.
سنگ آهک
به منظور کمک کردن ذوب و پایین آوردن دمای ذوب ناخالصیها به سنگ معدن افزوده میشود. نسبت تشکیل دهندههای بازی در مخلوط یعنی (CaO) و (MgO) به تشکیل دهندههای اسیدی یعنی (SiO2) باید در حد ثابتی حفظ شود تا تفالههای کف مانند و سبک (سیلیکاتهای کاسیم و منیزیم ) بطور کامل تشکیل شود و سایر ناخالصیهای همراه با خود را از آهن جدا کند. برای این منظور ، سنگ آهک و دولومیت بکار گرفته میشود.
گاهی برای کنترل ترکیب تفالههای جاری ، مقداری سیلیکات نیز بدان اضافه میشود. مناسبترین اندازه این دسته از مواد برای کورههای وزشی بین 70 تا 75 میلیمتر است.
واکنشهای کوره استخراج آهن
پس از اینکه کک در قسمت پایین کوره بارگیری شده ، آن را تا حدود گرم میکنند تا بر اثر وزش هوای گرم شروع به سوختن کرده ، دما را در دهانه قسمت سوخت کوره تا
افزایش دهد. دیاکسید کربن حاصل در این دما ناپایدار بوده ، بوسیله کک موجود در محیط به منوکسید کربن تبدیل میشود.بخار آب همراه با هوای داغ در واکنش با کک نیز خود تولید منوکسید کربن میکند.
واکنشهای انجام شده در دهانه سوخت که در حد بین مخزن سوخت و سنگ معدن آهن قرار دارد، در قسمت بالاتر کوره که دما زیر است، اکسیدهای آهن بوسیله منوکسید کربن و هیدروژن حاصل احیا میشوند. در قسمت بالاتر کوره وقتی که دما به
تا
رسید، سنگ آهک نیزتجزیه میشود. در قسمت پایین کوره دربالاتر از
اکسیدهای آهن بوسیله کربن احیا شده ، دیاکسید کربن حاصل بطور همزمان با کک واکنش داده و به منوکسید کربن تبدیل میشود.
این احیا به احیای مستقیم معروف است که نیازی به انرژی زیاد دارد. بیشتر گوگرد که همراه کک وارد کوره میشود، در داخل آن به تبدیل میشود.
حاصل با
ترکیب شده آنها را به
تبدیل می کند.
حاصل ضمن واکنش ، آهن آزاد میکند. میزان و چگونگی حذف گوگرد به دمای تفاله و نسبت
بستگی دارد.
احیای مستقیم
احیایی است که در آن ، سنگ معدن آهن ، بوسیله عوامل احیا کننده جامد یا گازی احیا میشود. با توجه به مقدار کربن موجود در آهن ، این عنصر بهصورت دو نوع محصول آهن یعنی چدن و فولاد عرضه میشود.
جدول نام و فرمول شیمیایی سنگ معدن های مهم آهن
فرمول شیمیایی | نام معدن شناسی | نام شیمیایی |
![]() | مگنتیت | تترا اکسید دی آهن (III) آهن (II) |
![]() | هماتیت | اکسید آهن (II) |
![]() | ایلمنیت | تری اکسید تیتان آهن (II) |
![]() | لیمونیت | ئیدروکسید آهن (III) |
- | - | یا اکسید آهن (III) هیدراته |
![]() | سیدریت (اسپاتیت) | کربنات آهن (II) |
![]() | چاموزیت ، گرینالیت | سیلیکات آهن (II) |
![]() | پیویت ، مارکالیت | دیسولفید آهن (II) |
آهن که مهترین فلز از نظر تجارتی است، بوسیله کاهش با کربن در کوره بلند صورت میگیرد. ارتفاع این کوره به حدود 30 متر و قطر آن به 7.5 متر میرسد و جدار داخلی آن بوسیله آجر مخصوصی که در برابر گرما مقاوم است، پوشیده شده است. این کوره چنان طراحی شده است که کار آن دائمی است. که عملکرد آن را مرور میکنیم. |
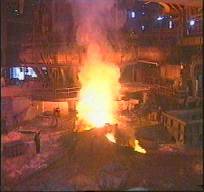
مراحل تولید آهن در کوره
از بالای کوره بلند ، کانه یا کانی آهن ، کک و سنگ آهک را که "گداز آور" یا "بار کوره" نیز مینامند، وارد میکنند و از پایین کوره نیز جریان شدیدی از هوای گرم میدهند. این هوای گرم گاهی با اکسیژن تقویت میشود. هوای ورودی با کک یا همان کربن ، ترکیب شده ، به کربن منوکسید کاهیده میشود و مقدار قابل ملاحظهای گرما آزاد میکند. در این مرحله دمای کوره بالاترین مقدار یعنی حدود 1500ċ را دارد.

بار کوره که در حال نزول است به تدریج گرم میشود. نخست رطوبت آن گرفته و سپس کانی آهن بطور جزئی توسط کربن منوکسید کاهیده میشود. در قسمت داغتر کوره ، کاهش کانی آهن به آهن فلزی ، تکمیل میشود و سنگ آهک نیز CO2 از دست میدهد و با ناخالصیهای موجود در کانی آهن (که بطور عمده سیلیسیم دیاکسید است) ترکیب شده ، سرباره مذاب تولید میشود. آهن مذاب و سرباره مذاب با یکدیگر مخلوط نمیشوند و در ته کوره دو لایه جداگانه تشکیل میشوند.
واکنشهای این مراحل عبارتند از:





در داغترین ناحیه کاهش به آهن فلزی صورت می گیرد:

نقش سرباره
لازم به ذکر است که سرباره مذاب عمدتا کلسیم سیلیکات است و بوسیله اثر نمایی گدازآور بر روی هرزه سنگ تولید میشود. این سرباره بر روی آهن مذاب شناور است و به این ترتیب فلز را از اکسید شدن بوسیله هوای ورودی حفظ میکند.نقش مقدار زیاد کک در کوره
واکنشهای کاهش اکسیدهای آهن برگشت پذیرند و کاهش کامل فقط وقتی صورت میگیرد که دیاکسید کربن حاصل را از بین ببریم. این کار توسط کاهش آن با مقدار زیاد کک صورت میگیرد.
گاز خروجی از بالای کوره
گازی که از بالای کوره خارج میشود، بطور عمده از منواکسید کربن و نیتروژن موجود در هوای دمیده شده ، تشکیل میشود. این مخلوط گازی داغ را با هوا ترکیب میکنند تا منواکسید کربن آن بسوزد و محصولات این احتراق را که گرمای بیشتری دارد از درون دستگاه تبادل گرما عبور میدهند و به کمک آن هوای ورودی را گرم میکنند.جایگزین هوا در بعضی از کورهها
در بعضی کورهها به جای هوا از اکسیژن نسبتا خالص استفاده میکنند. در این مورد ، ابعاد کوره کوچکتر و دمای آن قدری زیادتر است و مونواکسید کربن حاصل نسبت به مخلوط نیتروژن و مونواکسید کربن ، سوخت بهتری استسوختها ، در کوره بلند ، دو عمل را انجام میدهند : عمل ایجاد گرما و عمل احیا کنندگی و به دو دسته عمده طبیعی و مصنوعی تقسیم میشوند. سوخت مصرفی در این کوره بایستی دارای ارزش حرارتی زیاد بوده و در ضمن سوختن بهم نچسبند برای اینکه بتواند گازها را از بین خود عبور داده و عمل احتراق را تهسیل نماید بعضی از سوختهای طبیعی از قبیل زغال سنگ آنتراسیت و زغال سنگ قیری و لینیت ، بیشتر جنبه تاریخی دارند تا جنبه اقتصادی و از سوخت های مصنوعی که زغال چوب و کک میباشند ، کک اهمیت زیادی داشته و در اکثر کارخانه ها بکار میرود ، مزایای کک عبارت از تخلخل ، سختی ، فراوانی ، قابلیت احتراق بیشتر و ارزانی آن میباشد . برای تهیه کک باید چند نوع زغال سنگ را که مواد فرار موجود در آنها متفاوت میباشد ، با یکدیگر مخلوط و در کورههای مخصوص به کک تبدیل نمود . این عمل را کربنیزاسیون مینامند . ترکیب شیمیایی کک عبارت است از 94-85 درصد کربن و بقیه شامل مواد فرار ، خاکستر ، گوگرد و رطوبت میباشد . امروزه با پیشرفت تکنولوژی ، از سوختهای کمکی و تزریقی برای بهبود کارایی کوره استفاده می کنند برای مثال از تزریق پودر زغال جهت کاهش مصرف کک استفاده می شود و نتایج بدست آمده بسیار مطلوب بوده است ولی روش بهتر از این ، روش استفاده از مخلوط گاز طبیعی و نفت و یا مخلوط نفت با پودر زغال می باشد . وظایف و عملکرد کک در کوره بلند به شرح زیر است :
1. کک گداخته :
کک بایستی توسط اکسیداسیون جزئی به CO تبدیل شود و بیشترین انرژی گرمایی کوره را به وجود آورد .
2. احیا کنندگی کک :
کک دو عمل متفاوت احیا را انجام می دهد :
A . عمل احیا مستقیم جهت اکسیدهای دیر احیا شونده مثل احیا FeO و Ti و Si و ... ، مثلا : FeO + C = Fe + Co
B . عمل احیا غیر مستقیم که گاز CO به وجود آمده توسط اکسیداسیون جزئی کک با اکسید های عناصر احیا شونده وارد واکنش شده و اکسید های آن را احیا می کند ،
مثلاً :FeO + Co = Fe + C
3. عمل سمانتاسیون کک :
آهن گداخته و خمیری سعی دارد که در کنار کک اشباع گردد که این عمل باعث پایین آوردن نقطه ذوب آهن می گردد که در نهایت چدن مذاب کوره بلند بوجود می آید .
سمانتیت 3Fe + C = آهن اشباع از کربن ( چدن ) – Fe
در مورد عمل سمانتاسیون تکنولوژ کوره بلند هیچ گونه نقشی ندارد ، با عمل سمانتاسیون ( کربونیزه کردن ) نقطه ذوب آهن به طور مرتب پایین می آید تا به حد اشباع کامل برسد ، یعنی کربن در چدن به 4.3 % می رسد . البته کربن در چدن مذاب کوره بلند تا حدود 4.5 % و حتی بالاتر می رسد .
4. اثرات مستقل بودن کک :
کک یک سختی ویژه و مخصوص به خود دارد و در قسمت بدنه کوره هیچ گونه تغییر فیزیکی در آن داده نمی شود و نرم نمی گردد و بهترین شرایط را برای دیفوزین گازهای صعود کننده و عبوری را به وجود می آورد ، و به خصوص در منطقه خمیری و نرم شدن مواد کک نقش بسیار مهمی را بازی می کند ، زیرا کک در این منطقه به صورت جامد و گداخته باقی می ماند .
بنابراین به طور واضح بایستی در کیفیت و دانه بندی کک دقت بسیار زیادی کرد ، زیرا کک بیش از 50% حجم کل مواد شارژی را سهیم خواهد بود دیفوزیون گازهای صعود کننده در بدنه کوره از لابه لای کک ها نسبت به مواد آهن دار حدود 100-60 برابر خواهد بود .
سیاله ها و مواد گداز آور در کوره بلند ( آهــک )
سیاله ها ، موادی هستند که در کوره به جریان ذوب کمک کرده و جدا کردن ناخالصی ها از فلز مذاب را آسان می کنند . برای این منظور از آهک استفاده می گردد . آهک با ناخالصی های موجود در سنگ آهن مانند سیلیسیم ، منگنز و گوگرد ترکیب شده و آنها را بصورت سرباره به سطح مذاب می راند . آهکی که برای این منظور مورد استفاده قرار می گیرد ، بصورت سنگ آهک بوده و بایستی دارای ناخالصی های کمی نیز باشد .
هوای لازم برای ایجاد حرارت در کوره بلند
برای تحصیل یک تن آهن خام ، حدود 6-5 تن هوا لازم است که این هوا از مخلوط دو گاز اکسیژن و ازت به نسبت 1و 4 تشکیل شده است. در کورههای بلند جدید ، هوا بوسیله کمپرسورهای توربینی به داخل کوره دمیده میشوند . این توربینها با بخار یا برق کار کرده و فشار دم بیشتر و یکنواختی تولید میکنند . همچنین جهت تهیه هوای دم بعضی از کوره های بلند ، کمپرسورهای گازی نیز بکار برده میشود . در این ماشین ها ، گاز کورههای بلند همراه با هوا وارد ماشین شده و پس از متراکم شدن توسط جرقه الکتریکی آتش زده میشود و فشار حاصله باعث حرکت موتور کمپرسور میگردد .
هوای لازم برای احتراق و ایجاد حرارت در کوره بلند را با فرمول های خاصی اندازه گیری می کنند که به اختصار ، چند تا از آنها را برای شما می نویسیم :
1)درجه حرارت تئوری احتراق در جلو فورمهای هوای دم :
T0 : درجه حرارت ذوب ، Tw : درجه حرارت هوای گرم ، F : رطوبت هوای دمشی ،O2 : اکسیژن دمشی ، Ol : مازوت ، K : پودر زغال ، CH : گاز طبیعی ، W : مقدار هوای دمشی ، Ti : تولید چدن تن در ساعت ، T1 : درجه حرارت جلو فورمها
2) گاز تشکیل شده حاصل از واکنشهای جلو فورمهای هوای دم و مقدار هوای دمشی :
W=2.98×B-197
W : مقدار هوای گرم دمشی بر حسب متر مکعب بر تن چدن ، B : جمع کل مواد سوختی برحسب کیلوگرم بر تن چدن
3) فرمول محاسبه ی گازهای تولید شده بدون د نظر گرفتن گاز طبیعی :
F-form=Fkw×(1+Fo2z/Fkw+0.00248×windf)+1.243×10-3Föl
F-form : مقدار گاز جلو فورمها ، Fkw : مقدار هوای دمشی ، Fo2z : مقدار اکسیژن اضافی ، windf : رطوبت هوای دمشی ، Föl : مازوت
4) سرعت هوای دمشی از داخل فورم :
Vmw=[(Fkw+Fo2z)×(Tmw+273)]÷[273×Pmw×M×F×3600]
Vmw : سرعت هوای دمشی به داخل فورم (M/Sec) ، M : تعداد فورمهای دم یک کوره بلند ، F : سطح مقطع فورم (m2 ) ، Fkw : مقدار هوای دمشی طبیعی ، Fo2z : اکسیژن اضافی (m3/h) ، Tmw : درجه حرارت هوای دمشی ، Pmw : فشار هوای دمشی
یک قسمت از کارگاه های تکنولوژی کوره بلند به پارامترهای دمشی و گازی مربوط می شود که هر پارامتر ، خود به پارامتر دیگری بستگی دارد ؛ پارامترهای زیادی در کوره ی بلند قابل اندازه گیری و محاسبه هستند که به علت طولانی بودن در اینجا به بحث درباره ی آنها نمی پردازیم .
نحوه شارژ کردن مواد به کوره بلند
مواد به صورت لایه لایه درون کوره ریخته می شود و دارای دانه بندی مشخصی است از ریختن مواد ریز و گرد و غبار به داخل کوره پرهیز می شود زیرا این مواد در موقع دمش گاز موجب به اصطلاح خفه شدن کوره و پل بستن مواد می گردد مسئله مهم در باردهی این است که مواد به صورت ستونی در نیاید و توزیع مناسبی از مواد داشته باشد .
مواد توسط نوار نقاله به پایین کوره بلند حمل می گردند و از آنجا توسط بنکرهای مخصوص به دهانه کوره بلند حمل میگردند ؛ سیستم کار کوره بلند سیستمی دو زنگی میباشد . ابتدا مواد روی زنگ کوچک که دارای یک حرکت دورانی است ریخته می شوند این حرکت دورانی به توزیع بهتر مواد کمک میکند ، زنگ کوچک به طرف پایین حرکت کرده و مواد را روی زنگ بزرگ می ریزد . هنگام حرکت زنگ کوچک به طرف پایین زنگ بزرگ دهانه کوره را مسدود کرده است . به ازای هر چهار بار حرکت زنگ کوچک یکبار زنگ بزرگ به پایین حرکت کرده و مواد را درون کوره می ریزد . این سیستم دو زنگی موجب جلوگیری از اتلاف حرارت کوره و کنترل بهتر فشار درون کوره میگردد دراین حالت اتمسفر کوره تحت هیچ شرایطی با اتمسفر محیط در تماس مستقیم نمیباشد یعنی گاز کوره هنگامی خارج شود که زنگ بزرگ بسته شده و زنگ کوچک پایین می آید دراین حالت فشار در مابین دو زنگ بالا میباشد و پایین آمدن زنگ کوچک مشکل می شود که این فشار را می توان توسط لوله هایی از مابین دو زنگ تخلیه نمود . این بارگیری مداوم است و باید مواد به صورت مداوم پایین بروند .
فرآیند تولید آهن در کوره بلند و واکنشهای مربوطه
همانطور که گفته شد ، از بالای کوره بلند ، کانه یا کانی آهن ، کک و سنگ آهگ را که "گداز آور" یا "بار کوره" نیز مینامند ، وارد میکنند و از پایین کوره نیز جریان شدیدی از هوای گرم میدهند . این هوای گرم گاهی با اکسیژن تقویت میشود . با افزایش اکسیژن حجم نیتروژن کم میشود نیتروژن مقداری از گرما از قسمت های پایین کوره بالا برده و به بار میرساند و مقداری از آن را از دهانه خارج می کند . پس نمی توان N2 را کاملاً خارج کرد ولی با کاهش حجم آن می توان مقدار انتقال حرارت را کاهش داد . ارتفاع کوره به نحوی تنظیم شده است که انتقال گرما به خوبی صورت بگیرد . این حرکت ها مداوم است و اگر مداوم نباشد کوره دارای مشکلی بوده و باید با این پدیده مقابله شود . حرکت مواد با توجه به سطح بالایی آنها اندازه گیری میشود . اگر مواد به دیواره کوره بچسبند نزول آنها متوقف میشود یا ممکن است مواد به صورت پل قرار بگیرند در نتیجه پایین نمی آیند ؛ اگر اپراتور زود متوجه شود میتوان با اختلاف دمش به پل مواد ضربه زد و آن را شکست و اگر دیر متوجه شود ، مشکل آفرین است . طرز تشخیص این پل بستن بدین صورت است که دما در قسمت پایین کوره بیشترین مقدار دما را دارد و با افزایش ارتفاع کوره این دما به صورت تدریجی کاهش مییابد تا در دهانه کوره به کمترین مقدار خود میرسد اگر این کاهش دما در قسمتی ازکوره به یکباره اتفاق بیافتد نشان دهنده این است که در این منطقه مواد پل بسته اند که می توان آن قسمت از کوره را سوراخ کرد و با گذاشتن مواد منفجره این پل بستن را مرتفع نمود در غیر این صورت باید مواد داخل کوره بلند را تخلیه کرده و مواد را خارج نمود که این خود مستلزم هزینه و وقت زیاد میباشد . کنترل فشار در کوره بلند ازاهمیت بالایی برخوردار است زیرا این کنترل فشار پایین آمدن مواد و انجام واکنش های ترمودینامیکی داخل کوره را تنظیم میکند . فشار در پایین و بالای مواد توسط شدت هوای دمیده شده و خروج گازها در بالای کوره کنترل می گردد .
وقتی که هوای پیش گرم شده که دارای درصد بالای اکسیژن است با فشار 5/2 تا 3 اتمسفر به داخل کوره دمیده می شود در مرحله اول ورود به کوره چون دارای فشار جزیی بالای اکسیژن است C+O2=CO2رخ می دهد این واکنش یک واکنش گرما زا می باشد و باعث ذوب مواد جامد می گردد . این واکنش بیشتر در جداره و مناطق نزدیک به جداره رخ می دهد . دما در این منطقه در حدود 1800 درجه سانتی گراد است ، در این دما فاز CO پایدار است ولی چون فشار جزیی اکسیژن ورودی بالا است واکنش در جهت تولید گاز CO2 پیش میرود . ولی با حرکت از جداره به طرف مرکز کوره نسبت CO به CO2 بیشتر میشود این بدان علت است که اکسیژن ورودی مصرف شده و فشار جزیی آن کاهش پیدا می کند با کاهش اکسیژن واکنش به سمت تولید گاز CO پیش می رود تولید گاز CO یک واکنش گرما گیر است و بیشتر در مناطق مرکزی کوره رخ میدهد . CO2 تولید شده نیز چون در این دما ناپایدر است طبق واکنش C+CO2 =2CO تبدیل میگردد فشار هوای دمیده شده باعث صعود گازهای تولید شده به سمت بالا میگردد . به این واکنش که تعادل میان CO و CO2 را در کنار کربن مشخص می کند و تابع دما و فشار است ، واکنش بودوارد می گویند .
با افزایش ارتفاع در کوره بلند دما کاهش می یابد با کاهش دما نسبت CO به CO2 کمتر شده تا اینکه در بالای کوره بلند بیشترین مقدار CO2 وجود دارد . در یک نسبت مشخص CO و CO2 در یک ارتفاع مشخص در کوره گاز CO می تواند اکسید های فلزی را احیا کند .
در این مرحله ، کاهش کانی آهن به آهن فلزی ، تکمیل میشود و سنگ آهک نیز CO2 از دست میدهد و با ناخالصیهای موجود در کانی آهن (که بطور عمده سیلیسیم دیاکسید است) ترکیب شده ، سرباره مذاب تولید میشود . آهن مذاب و سرباره مذاب با یکدیگر مخلوط نمیشوند و در ته کوره دو لایه جداگانه تشکیل میدهند.
نقش سرباره در کوره بلند
همانطور که می دانید ، سنگ آهك براي بهتر كردن خواص كلوخه بدست آمده و بهبود عمليات كوره بلند و سرباره گیری مورد استفاده قرار می گیرد . سرباره ، عبارتست از ماده مذابی که بر اثر فعل و انفعال بین مواد گداز ، سنگ آهن ، سوخت و ناخالصیهای اکسید موجود در فلز بوجود میآید و در اثر این فعل انفعالات ، ناخالصیهایی که نباید در چدن وجود داشته باشد ، از آهن خام جدا میشود . مواد متشکله اصلی سرباره عبارت است از MgO , Al2O3 , SiO2 , CaO که جمعاً 90 درصد سرباره را تشکیل میدهند ، 10 درصد بقیه عبارتند از CaS , MnS, MnO , FeO و غیره . لازم به ذکر است که سرباره مذاب عمدتاً کلسیم سیلیکات است و بوسیله اثر نمایی گدازآور بر روی هرزه سنگ تولید میشود . این سرباره بر روی آهن مذاب شناور است و به این ترتیب فلز را از اکسید شدن بوسیله هوای ورودی حفظ میکند . معمولا حجم سرباره ای که از کوره بلند به دست می آید، سه برابر حجم آهن خام تولیدی می باشد . از سرباره کوره بلند برای تهیه آجرهای نسوز ، سیمان ، عایق حرارتی شبیه پشم شیشه ، کود شیمیایی و زیر سازی جاده ها استفاده می کنند .
گاز های خروجی از بالای کوره بلند
گازی که از بالای کوره خارج میشود ، بطور عمده از منواکسید کربن و نیتروژن موجود که در هوای دمیده شده ، تشکیل میشود . این مخلوط گازی داغ را با هوا ترکیب میکنند تا منواکسید کربن آن بسوزد و محصولات این احتراق را که گرمای بیشتری دارد از درون دستگاه تبادل گرما عبور میدهند و به کمک آن هوای ورودی را گرم میکنند. البته در بعضی کورهها به جای هوا از اکسیژن نسبتاً خالص استفاده میکنند . در این مورد ، ابعاد کوره کوچکتر و دمای آن قدری زیادتر است و مونواکسید کربن حاصل نسبت به مخلوط نیتروژن و مونواکسید کربن سوخت بهتری دارد .
محصولات کوره بلند
محصولات کوره بلند را آهن خام می نامند . آهن خام دارای 3 تا 4 درصد کربن بوده و نقطه ذوب آن در حدود 1300 درجه سانتی گراد می باشد این محصول را به دلیل شکنندگی زیاد و ناخالصی های فراوان نمی تواند در صنعت مورد استفاده قرار داد . آهن خام بخاطر داشتن کربن زیاد ، قابلیت شکلپذیری ، جوشکاری و چکش خواری را ندارد ، بنابراین لازم است طی عملیاتی مقدار کربن آن را کاهش داده و سایر عناصر موجود در آهن خام مانند گوگرد ، فسفر ، سیلیسیم و منگنز را به حد قابل قبولی رساند . همانطور که گفتیم ، از کوره بلند محصولات فرعی دیگری نیز به صورت سرباره و گاز به دست می آید .
اختلالات و مشکلات استفاده از کوره بلند
محاطی کار کردن کوره بلند :
عبور بیش از اندازه گاز از کناره دیواره کوره نسبت به حالت نرمال کارکردن کوره ، محاطی کارکردن کوره بلند می نامند ، اگر مواد شارژی با دانه بندی بزرگتری در کناره ها شارژ گردد ، درصد تخلخل مواد در کناره ها بیشتر شده که باعث پدیده فوق میگردد . پدیده فوق حاصل از کمبود هوای دمشی و یا افزایش قطر فورم ها و کاهش سرعت هوای دمشی در فورم ها و افزایش درصد مواد ریز بخصوص در مرکز کوره بوجود می آید .
یکطرفه کار کردن کوره بلند :
اگر اختلاف سطح مواد در سمت چپ و راست کوره و یا شرق و غرب کوره قابل ملاحظه باشد به یکطرفه کار کردن کوره معروف می باشد .
مرکزی کار کردن کوره بلند :
اگر بارگیری مواد آهن دار و بخصوص ریز در کناره کوره و مواد درشت بخصوص کک در مرکز کوره بیشتر شارژ گردد به طوری که درصد تخلخل مواد در مرکز کوره نسبت به کناره ها خیلی بیشتر باشد جریان صعود گازها بعلت مقاومت کم مواد از مرکز کوره عبور می کند و به هر علتی که مواد مرکزی تخلخل بالایی داشته باشد این پدیده بوجود می آید .
بیرون زدن تفاله در حین خروج :
مخلوط کک های نسوخته و ریز با سرباره غیر آماده و مقدار چدن که با هم آغشته شده اند و در بعضی از خروج ها از مجرای چدن بیرون می زند را تفاله می نامند .
از مشکلات استفاده از روش کوره بلند در ایران وابستگی آن به کک و مشکل بودن تامین آن در کشور است .
منابع و مآخذ
کتاب کنترل فرایند تولید و اختلالات در کوره بلند ، ترجمه ثانی آبدینی
| نسخه قابل چاپ | تعداد بازديد : 9766 |